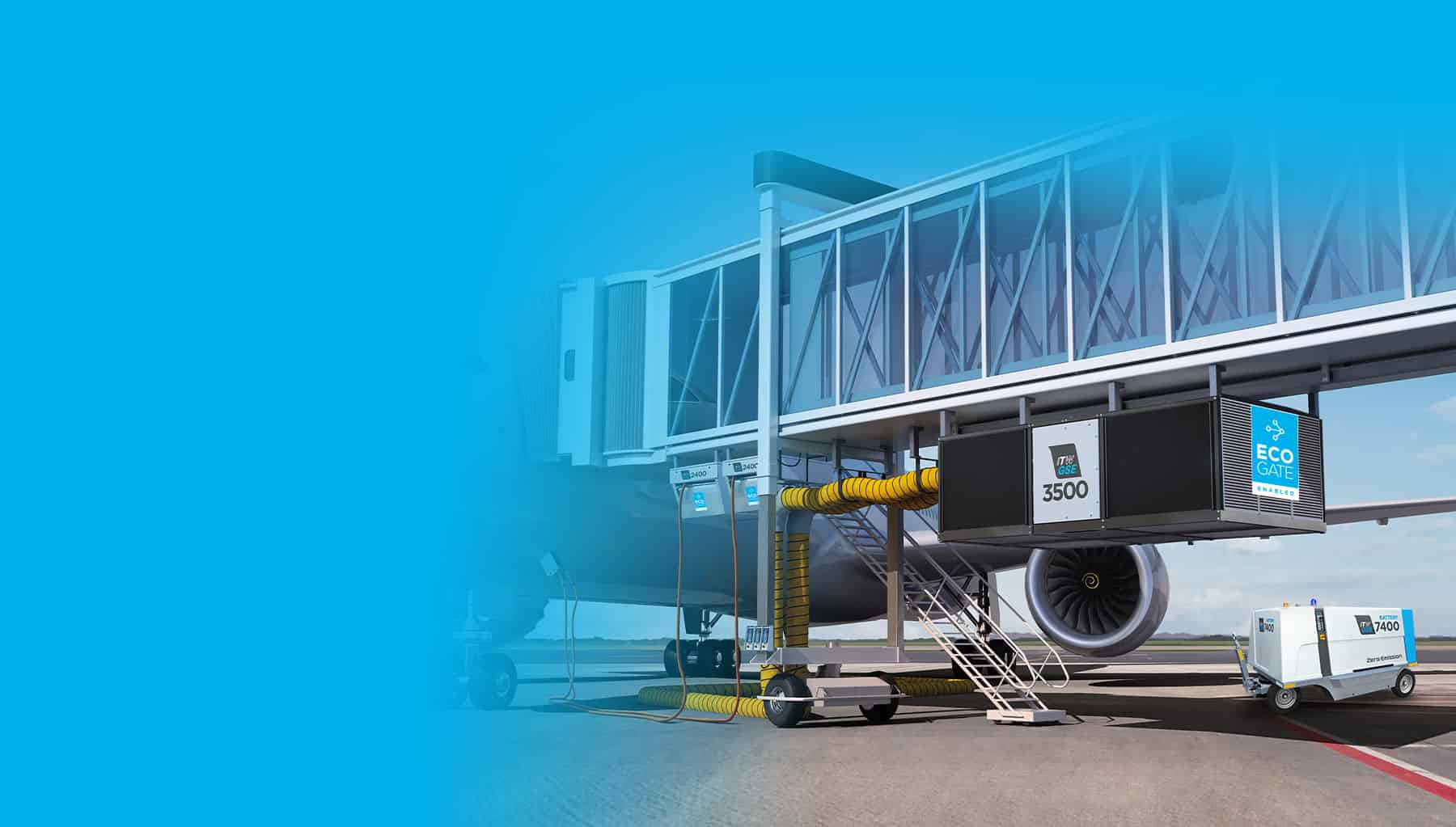
Simply Smarter Ground Support
ITW GSE covers your needs no matter which type of ground power unit or pre-conditioned air unit you are looking for. We also supply cables and hoses. We got you covered!
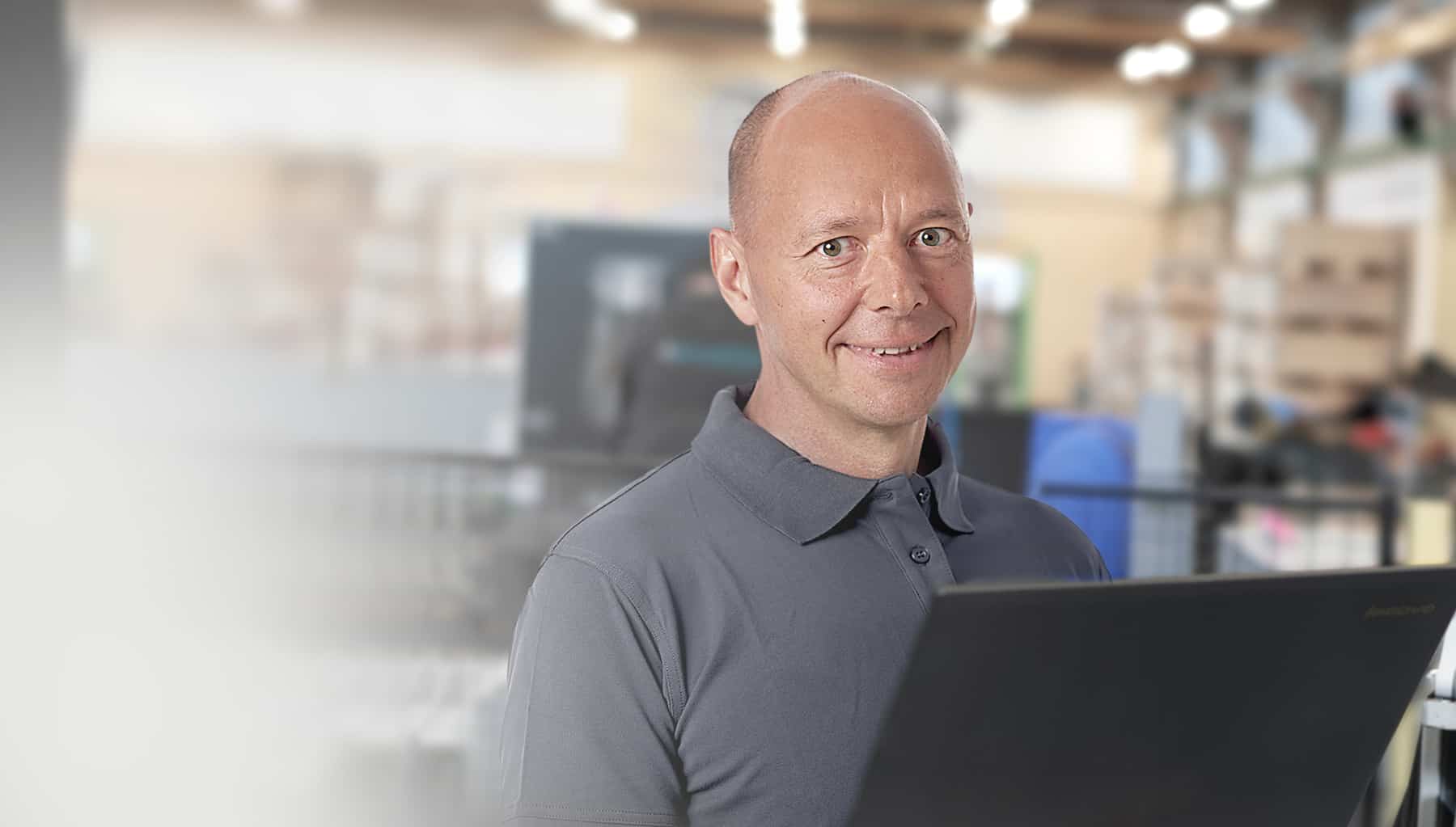
Engineering is in our blood
We supply the aviation industry with the cleanest, most reliable and cost-efficient Ground Support Equipment.
The leading supplier of Ground Power Units, Pre-Conditioned Air Units, Cables and Hoses
ITW GSE combines customer-back innovation with an in-depth knowledge of the Ground Support Equipment industry to develop and deliver solutions tailored to your needs.
We strive to make best-in-class even better.
We have delivered more than 90,000 units to customers in over 100 countries.
That is experience you can count on.
Customer Support
How can we help you?
Need schematics, spare-part lists or instructional videos? Use the ‘Product Assistance’ button.
Questions for Customer Support? Use the ‘Contact Customer Support’ button.
If your question involves a specific product, please provide the product’s serial number.
News and exhibitions
Celebrating a Century of Innovation and Commitment
Recently, we had the pleasure of welcoming the editor of GHI magazine, Samantha Payne Polepaka, to our Danish facility. She was there to interview...
How EcoGate can ease charging challenges
Do you ever wonder how you can scale battery powered ground power units to a larger fleet? One of the questions we often hear...
100 years anniversary celebration for the Danish ITW GSE facility
Hip-hip hooray! Our Danish facility is turning 100 years and we have of course been celebrating! The celebration included a team breakfast in the...
96th Annual AAAE – Taking Flight Towards a New Horizon
With such a diverse audience of industry leaders how could you miss this event. Industry solutions, continuing education, and certifications. You will definitely find…
You can count on us
ITW GSE combines customer-back innovation with an in-depth knowledge of the GSE industry to develop and deliver solutions that are tailored to your needs.
We strive to make best-in-class even better. As a result, you get cleaner and more reliable ground support systems that improve the working environment for your staff and increase the efficiency of your operations.
We provide experience you can count on.
Read moreCareers at ITW GSE
ITW GSE employees have a strong sense of belonging. We work as a team and learn from each other. We focus on what we do best and we do it better than anyone else.
Our corporate values and the dedication of our workforce is the cornerstone of our success.
Join us